Simple Secrets To Speed Up On How To Test
Electronic Components-Part I
If you are
in the electronic repair line you would know that checking
electronic components in electronic boards can take up lots of your
time especially if you do not know the short cut way to test it.
Many of us when starting in the field of electronic repair check
each electronic component one by one by removing it out from the
board. This is the right way to test electronic components but it
is very time consuming.
For example, if you already confirmed
that the power supply section is the main cause of the problem in
electronic equipment, you may take about 30-45 minutes to scan
through all the electronic components in the section but for some
senior or experienced repair technicians, they can check all of the
electronic components in less than 15 minutes and accurate too!
Wow, that was almost half of the time you spent on checking
them.
This is a big different in terms of
efficiency of how many equipment you can repaired in a day. In
other word, if you can solve a problem fast, you can actually
repair more equipment in a day and more profit to you. Wouldn’t it
be great if you can have the skills like the super tech? Or you may
ask “Is there a way to actually cut short the process of testing
electronic components and at the same time produce accurate result?
Yes there is, in this article I’m going to show you how you can
speed up the process of testing electronic components. Let’s
start!
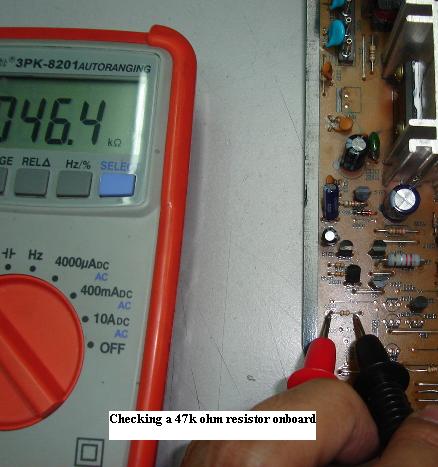
We will start with resistor first.
Normally the right way to test a resistor is to desolder out one
lead and then measure with digital multimeter (please don’t use
analog meter as it won’t show you a precise reading). Do you know
that you can actually check a resistor while it still on board?
This is true especially when the test voltage output from your
digital meter is less than 0.6 volt as it would not trigger the
surrounding semiconductors like the transistors, diodes and
integrated circuits (IC). If it is more than 0.6 volt then you may
not get an accurate result because your meter had triggered the
surrounding semiconductors. Another thing you need to know is that
if the resistor that you are checking on board parallel with
another resistor, you will not get an exact reading. Let’s take
this for example, assuming you are checking a 470 ohms resistor on
board and the measurement you get was 200 ohms plus, this means the
resistor could have been parallel with another resistor (back
circuit) or surrounding circuit. If you get 0 ohms, this is very
obvious that the resistor have open circuit. What if you get 2.2
megaohms? This resistor is either open or has gone up in value.
Other circuit components cannot possibly increase the value of a
resistor; any back circuit could only make the resistance reading
lower!
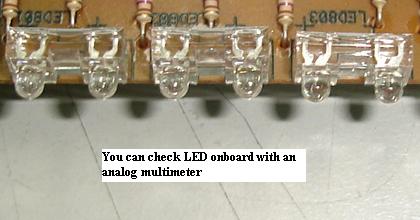
Light emitting diodes or LED is very
simple to check. Just connect your analog meter probe to the pins
of LED and set your meter to X1 ohm. If there is no light from the
LED, just change the polarity of the probes. You can check LED
while it is still in circuit.
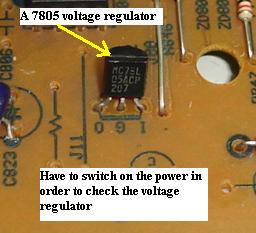
Voltage regulator can’t be check off
board with multimeter because it is an IC (it has lots of
components inside it). You have to switch “ON” the equipment and
check the output dc voltage of the voltage regulator. First you
must know what the part numbers of the voltage regulator are, and
then you read the specification and locate the input and output
voltage and pins. For example, the general type of voltage
regulator starts with the part numbers like 7805, 7812, 7908 and
etc. From the spec you would know that pin one is input, pin 2 is
ground and pin 3 is output. If there is input voltage to the
voltage regulator and no or low output voltage, suspect the voltage
regulator itself faulty or something along the output line that
dragged down the output voltage. Do you still remember from my
previous article that voltage regulator can breakdown when under
full load? Since the voltage regulator is easily available and
cheap, just direct replace it and retest the equipment or recheck
again the output voltage.
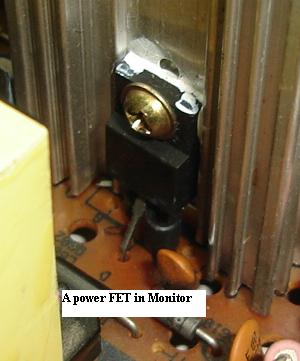
Many switch mode power supply are using
the combination of a power FET and a PWM IC design to switch the
power transformer. Whenever there is any power failure (fuse
totally blown into dark color) one will always suspect the power
FET has gave way. Usually we would use the black probe set to X 1
ohms and place it to the center pin (drain) and the red probe to
the gate and the source pin. This is the same way when we want to
check HOT on board. If there is a reading, chances are high that
the FET has developed a short circuit. But you also have to
remember that a shorted bridge rectifier may cause the power FET to
have reading when check with the analog meter while it still on
board.

If you get an open reading this doesn’t
mean the power FET is good because a faulty FET can become open
circuit too. My point to you here is that don’t waste your time
checking FET onboard (if the FET shorted then you can detect right
away but what if the FET open circuit?) because it is not accurate,
you have no choice when comes to testing FET, you just have to
remove it out from board and test it with analog meter set to X 10k
ohms (refer back to my website www.electronicrepairguide.com about
testing FET). This is true also if you want to check FET in the B+
circuit (B+ FET) and FET’s in the Monitor S-correction
circuit.
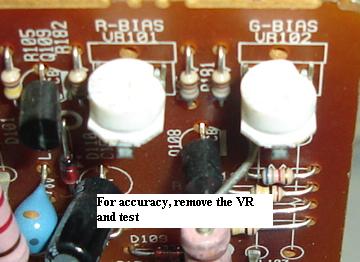
Checking variable resistor (VR) on board
is not that accurate because of the back circuit besides some VR
have their resistance code printed so small at the bottom of the
VR. The best is still removing it out from the circuit and test it
with an analog meter. Any erratic reading can be easily seen from
the analog meter panel compares to using digital meter.
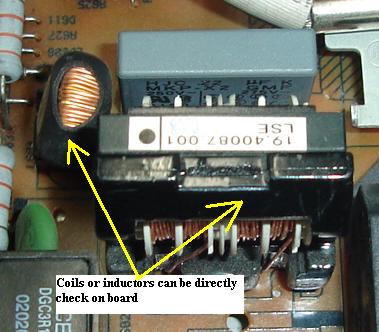
Inductor or coil testing can be done on
board without removing the coil out from the circuit board. If a
coil has less loops (small coil), then we can just direct measure
it with our normal ohmmeter. A small coil is just like a wire or a
jumper and it rarely become defective although it has some
inductance value in it. Testing coils that have a bigger inductance
value like the B+ coil used in Monitor circuit is different from
checking the small coils. You can’t just measure the bigger coils
with an ohmmeter because a bigger coils tends to develop short
circuit internally that can’t be detected by a normal meter. The
meter that I use to check the bigger coils is the Dick smith
flyback tester. You can check the coils while it is still in the
circuit. Once you know the right method of testing coils, I’m sure
it won’t take you long to measure any coils in electronic
board.
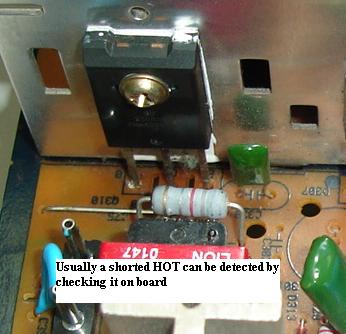
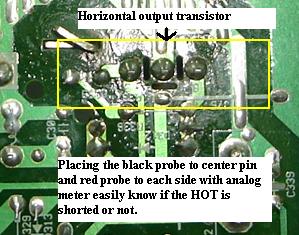
Checking horizontal output transistor is
so easy and you can check it on board. Set your analog meter to X 1
ohm and place the black probe to the center pin (collector) of the
HOT and the red probe to base and emitter. It should not register
any reading. If there is a reading, most probably the HOT has
developed a short circuit. Be aware too that components that links
to the HOT like damper diode, flyback transformer, safety
capacitor, B+ circuit components and if these components go shorted
it could cause your analog meter to have reading. Some HOT in
certain Monitor designs are difficult to open (you have to remove
the whole board in order to unscrew the HOT) so to save time follow
the example above.

As for the switch mode power transformer
(SMPT) primary winding, you can’t accurately check it with an ohms
meter even if you already took it out from the board. You can only
test it with a special type of coil meter or the dick smith flyback
tester. You can check the primary winding of the SMPT on board
without removing it out with the flyback tester. If there are any
shorted components in the primary side (power fet) or in secondary
side (secondary output diodes) the flyback tester will registered a
shorted reading and the LED bars would not lit. Just play around
with the flyback tester (if you have one) and I believe you will
quickly notice how it can help you to test a winding fast. Some
technicians are using the more expensive type of flyback tester
such as the Sencore LC 103 capacitor and inductor analyzer to test
the primary winding of SMPT.
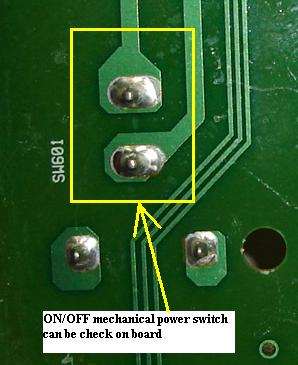
Checking the on/off power switch is the
easiest one. Just place your meter probes to the switch point
(assuming the power switch have 2 leads) and set your ohm meter or
continuity check function. It should show a very low ohm resistance
or the beeper will beep if you use the continuity checker. You can
perform this test even if the power switch is still in circuit. You
can also use this method to test on the micro switch.
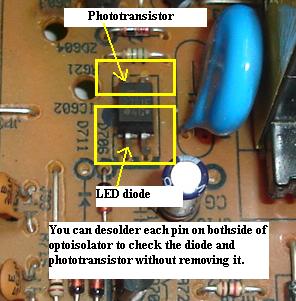
Optoisolator or optocoupler IC’s usually
located in between the primary and secondary side of power supply
and can be test even if the IC is still on board (you can actually
test this type of IC with your multimeter). Some of the famous
optocoupler part numbers are 4N25, 4N35, PC123 and etc.
Just desolder
one pin on each side (assuming this optocoupler have 2 pins
on each side) of the optocoupler. Pin 1 and 2 is the LED
light and pin 3 and 4 is the phototransistor collector and
emitter. Place your analog meter probe set to X10 k ohms at
pin 1 and 2 either way and it should show only one reading
(low resistance reading). This is just the exact same way as
when you are checking a normal diode. If it shows 2 reading
most probably it had developed a short circuit. Now place
your probes to pin 3 and 4 either way and again it will only
show one reading (this time the resistance reading is a
little bit high). If you got two readings then the internal
transistor may have short circuit.
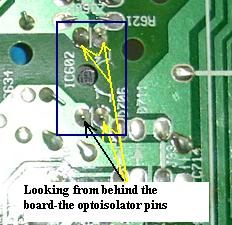
If you want to measure an optocoupler
that have 6 or even 8 pins, I suggest that you search for its data
first from the internet or from semiconductor data book. Once you
know how the internal components are wired, then you will use the
best checking method to test them individually. Remember, a shorted optoisolator
can cause low power, no power or even power blink in switch mode
power supply.
This is the end of part one article and
part 2 will be reaching your mailbox by next week. I’ll be touching
on components like the flyback transformer, capacitors, diodes,
zener diode, posistor, yoke coils, transistor and many more. Have a
great week my friend!
|